Sustainability at BMW.
With a systematic sustainability strategy, the BMW Group is setting new benchmarks in the automotive industry.
For the BMW Group, sheer driving pleasure extends far beyond mobility. This is because the topic of sustainability is a key issue for us, and one in which we make no concessions. On the contrary, we are entering the future with a completely new and consistent strategy that not only extends beyond our direct sphere of influence but also raises the topic of sustainability to an entirely new level. In the past years and decades we have already set significant standards in the life cycle assessment of our vehicles - starting with the resources used, through energy consumption, to the recycling rate. In the coming years, we will continuously expand our far-reaching electrification strategy and offer 25 electrified models in 2023.However, the goal of climate neutrality and emission-free mobility can only be achieved through a variety of electrified drive technologies. For this reason, and in order to achieve even greater flexibility with regard to the needs of our customers, we will continue to drive forward our commitment to the development of hydrogen fuel cells in a technology-neutral approach. We have already presented the BMW i Hydrogen NEXT at the IAA 2019. In the next step, we will present a small series of the BMW i Hydrogen NEXT in 2022. Step by step, we are thus breaking new ground towards an environmentally friendly and emission-free future.
" WE DON'T DO SUSTAINABILITY AT BMW. WE MAKE BMW SUSTAINABLE. “
Oliver Zipse – Chairman of the Board of Management of BMW AG
SUSTAINABILITY IN THE BMW iX.
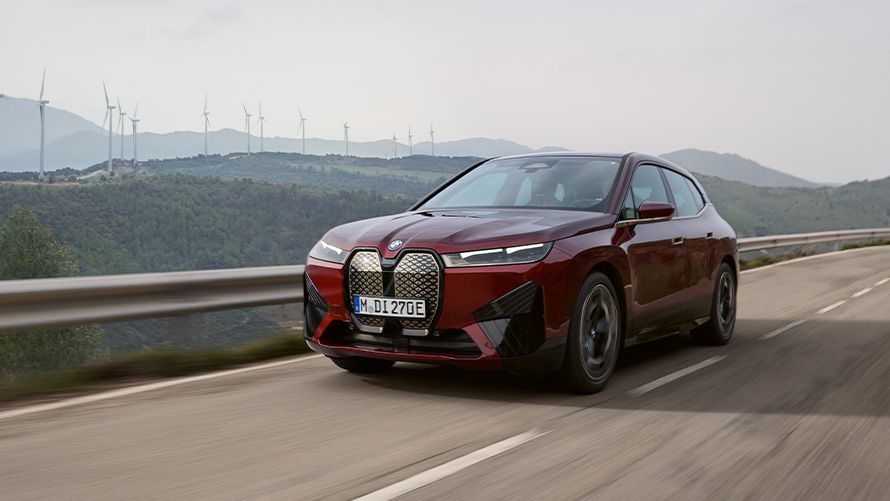
SETTING THE COURSE IN THE VALUE-ADDED CHAIN.
We know how to think of sustainability holistically. This is why we apply leverage during the development and production of our vehicles. Our goal is a sustainable value chain that covers its own needs with recyclates and renewable raw materials - including energy supply. Admittedly, we have not arrived there yet – but have already achieved pioneering successes on the way. It is not only the handling of resources that plays such a key role in BMW Group business model, but also the reduction of CO2 emissions. Due to the increasing proportion of electrified models and the manufacture of their high-voltage batteries and intensive use of energy and resources this entails, we have to integrate particularly far-reaching measures along the value added chain with respect to reducing CO2. Among the measures to achieve this, the BMW Group will be establishing the CO2 footprint for the material supply chain as a criterion to be considered when awarding contracts to suppliers and will thus be assuming a pioneering role as the first car manufacturer with specific CO2 targets for its supply chain. After all, if we failed to do this, the increasing electrification would result in a sharp increase in CO2 emissions in the supply chain. We are initiating the turnaround and have set ourselves the target of lowering CO2 emissions in the supply chain in the year 2020 by 20% compared with 2019.
20%
reduction in the CO2 emissions generated in the supply chain of the BMW Group per vehicle produced by 2030. Without our measures, the increasing electrification would lead to a 40% rise in CO2 emissions within the supply chain for each vehicle produced. We are initiating the turnaround.
PRODUCTION RECONCEIVED.
With the signing of the United Nations Environment Programme, the "International Declaration on Cleaner Production", in 2001, we committed ourselves to keeping environmental impacts and resource consumption in our worldwide production as low as possible.
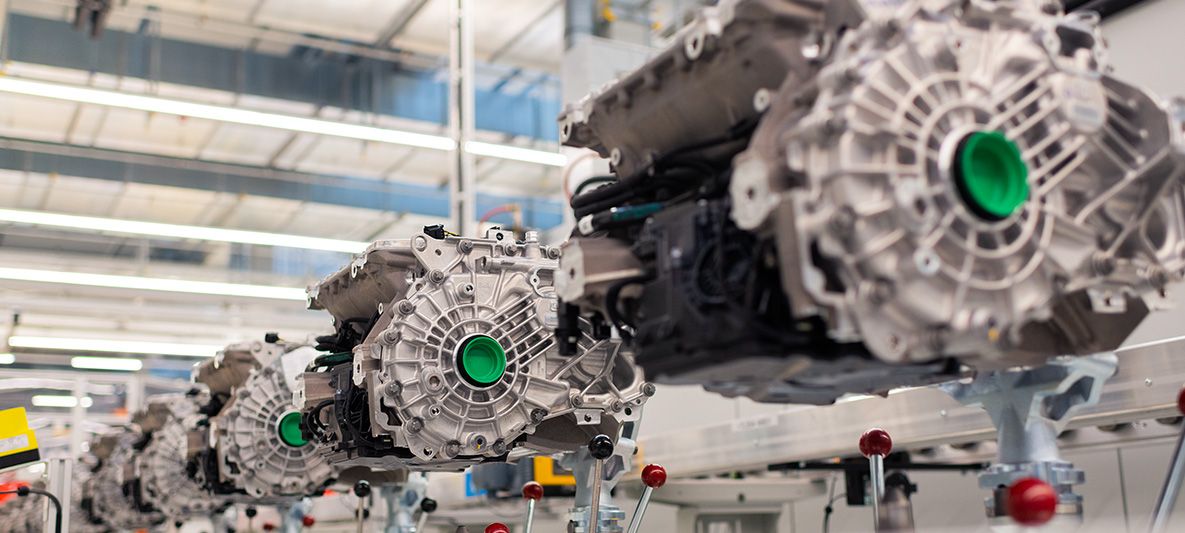
USE OF SUSTAINABLE MATERIALS.
The BMW Group with its locations and plants is already a benchmark in resource efficiency with regard to low CO2 emissions. Because we do not only want to be part of a sustainable future - we want to be the driving force behind it. We have therefore set ourselves the highest targets in the industry for the year 2030. In order to monitor and analyse our far-reaching measures, we have introduced environmental management systems at all our existing production sites, which are constantly being developed and optimised. Only in this way can we fulfil our ambition of being able to demonstrate the efficacy of our standards and regulations. Alongside the continuous expansion and use of renewable energies and regenerative raw materials in our production, we are also setting an important course with our recycling operations. Today, 99% of the waste generated by our global internal production of 2.5 million vehicles annually is recycled and recovered. And we are constantly working on raising this bar still higher.
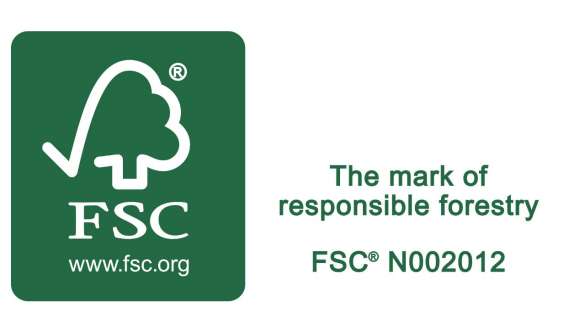
FSC certified wood.
The BMW Group works together closely with the Forest Stewardship Council (FSC) and is actively committed to responsible and sustainable forestry by adhering to the strict standards. The decorative trim of the instrument panel in the BMW i3, for instance, is made of FSC-certified eucalyptus wood.
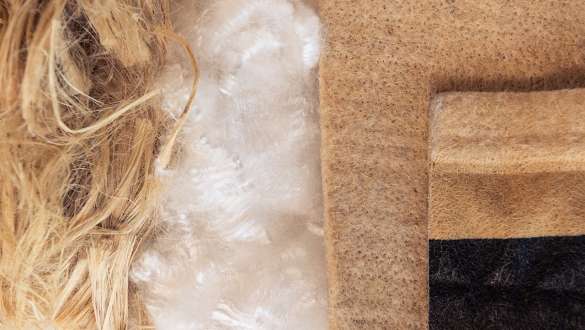
Kenaf.
Kenaf is a plant from the hibiscus family with fibres that are put to a wide range of commercial uses. The interior of the BMW i3 comprises 30% kenaf and consequently sets standards within automobile production for the sustainable deployment of resources.
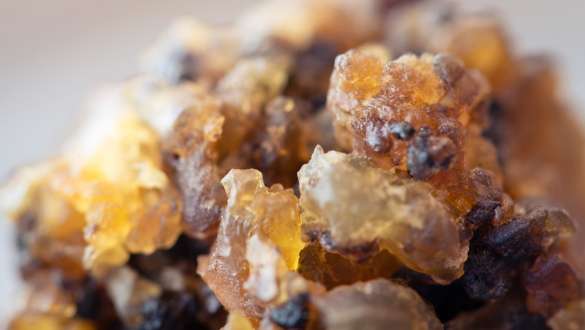
Natural Rubber.
As the first car manufacturer worldwide, the BMW Group is starting to equip its vehicles with tyres made from sustainably grown natural rubber. The BMW X5 xDrive45e plug-in hybrid (fuel consumption combined: 1.7 - 1.2 l/100km (WLTP), 2.1 - 1.6 l/100 km (NEDC); electricity consumption combined: 27.7 - 24.3 kWh/100 km (W ...
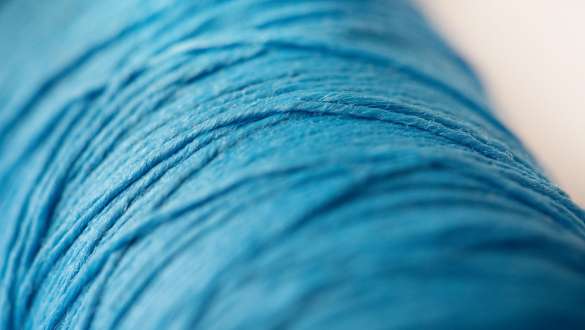
Econyl.
The recycling of primary materials represents an important measure of holistic sustainability within the BMW Group. A good example of recycled materials meeting our premium standard in terms of their quality is the use of Econyl. It is nylon yarn that is extracted from nylon waste in a special process and is used, for ...
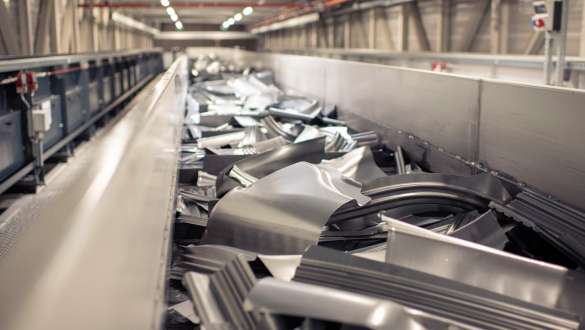
Aluminium.
Alongside steel, aluminium is the most important resource for production within the BMW Group. A correspondingly high value is attached to the entire value added chain in terms of efficiency relating to resources and energy. As a founding member of the Aluminium Stewardship Initiative (ASI), the BMW Group actively enga ...
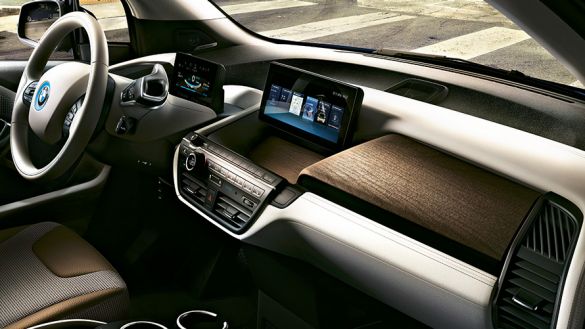
RECYCLING AS A KEY FACTOR.
On the way to sustainable, resource-saving and future-proof production, the recycling of materials is an essential factor, which we use as leverage. Alongside the intelligent planning of our products, the reuse of materials in the form of recycled substances is also firmly anchored in our value-added chain. All in all, we can now already recycle the waste generated in our internal production to a level of 99%.
SUSTAINABILITY IN THE BMW iX.
As a vehicle, the BMW iX is setting new standards in sustainability. Based on greenhouse gas emissions over a vehicle’s entire life cycle, the BMW iX generates 45% fewer emissions than a comparably powered SAV with a diesel engine – thanks to a holistic approach. Measures such as the use of 100% renewable energy in production contribute to this, or the transparently purchased raw materials all along the supply chain. Sustainability is also tangible in the BMW iX in the form of natural or recycled materials. The leather of the interior, for example, has been tanned using a natural olive leaf extract and is free of chrome residues. The control island of the optional 'Clear & Bold' specification is made of FSC-certified wood, while the floor trim and floor mats are made of Econyl.
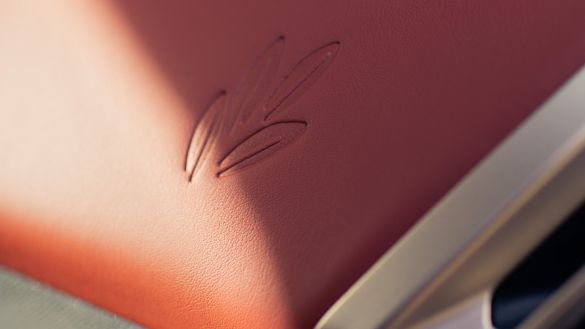
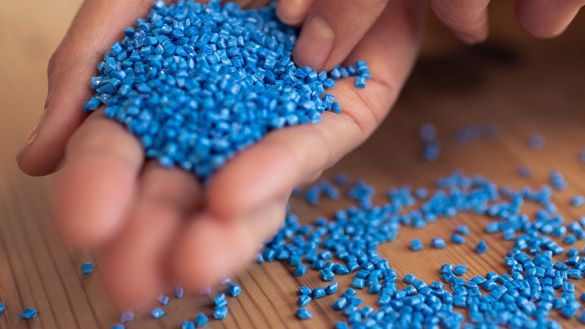
RECYCLATES.
Whenever it makes technical, ecological and economic sense and is feasible, we use recycled and renewable raw materials – and aim to significantly increase the proportion of such materials by 2030. In the case of our two most important resources, we are aiming for a factor of 4-6 for aluminium and a factor of 2-5 for steel. Today we already use around 25% secondary steel, up to 50% secondary aluminium in certain components and up to 20% secondary thermoplastics. In this way, we are committed to life cycle engineering for efficient recycling, because the use of secondary materials reduces the CO2 footprint considerably.
RECYCLING OF OUR END-OF-LIFE VEHICLES.
Even when the journey is over for a BMW, it still remains an important constituent of the value-added chain. After all, we do not regard our end-of-life vehicles, their individual components and materials as waste to be disposed of, but as an essential source of secondary raw materials. In 30 countries and together with their national sales companies, we have already regulated the take-back of end-of-life vehicles for this purpose and offer environmentally compatible recycling at more than 3,000 take-back points worldwide. Above all, we want to ensure that our electric vehicles are recycled transparently. In the long term, electric mobility cannot rely on primary materials alone, which is why the underlying flow of resources must change. Our customers therefore have the option of returning their vehicles to the Munich Recycling and Dismantling Centre (RDZ). Here, in addition to accepting end-of-life vehicles, we are constantly working on new concepts and measures to continuously develop our recycling processes.
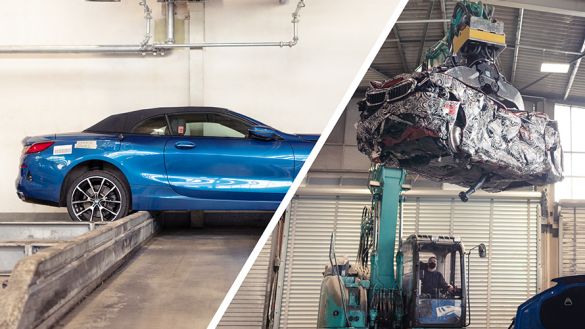
EFFICIENT ENERGY GENERATION.
The BMW Group has a direct influence on the CO2 emissions of its own plants and locations and already represents a benchmark there in terms of resource efficiency. By the year 2030, we aim to reduce the CO2 emissions of our locations by 80%. To this end, we have been obtaining our entire external electricity from renewable sources. And, as from 2021, our plants and locations will become completely climate-neutral: firstly, by reducing overall energy consumption and, secondly, by then only using renewable energies that we have generated ourselves to the greatest possible extent. To achieve this, we are systematically investing in optimising the energy efficiency of our locations and are conducting on-site examinations on the best way to obtain energy –
such as whether it be through the use of hydrogen, biogas, biomass or geothermal energy. The use of green hydrogen can also play a key role here at suitable locations, and we are currently in the process of examining its efficiency for heat generation in a pilot plant. At the same time, we are optimising the energy efficiency of our production: we are reducing the demand for heating, by reusing more waste heat from processes and securing thermal cycles. The use of digital techniques such as data analytics enables us to reduce electricity consumption through intelligent control and simultaneously minimise the quantity of scrap parts.
SUSTAINABILITY PRACTISED IN OUR PRODUCTION PLANTS.
BMW Group Plant Leipzig.
This air is full of efficiency – the BMW Group plant in Leipzig is one of the most modern and sustainable vehicle production sites in the world. Since 2013, automobiles with an electric drivetrain and CFRP lightweight chassis have been rolling off the production lines here. The plant is the first car factory in the whole of Germany to be working to a considerable extent with electricity from four purpose-built wind turbines on site. With the innovative battery farm comprising about 700 BMW i3 high-voltage batteries, we are pursuing a number of measures at once in order to achieve efficient resource and energy management in production. Firstly, we are constantly working on extending the life of batteries. Secondly, the battery farm stores surplus energy from the wind turbines when supply exceeds demand and can then feed in this surplus when the electricity supply is too low. In this way, we are contributing to the stability of the public power grid.
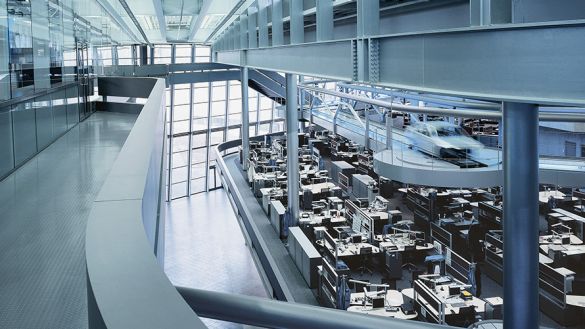
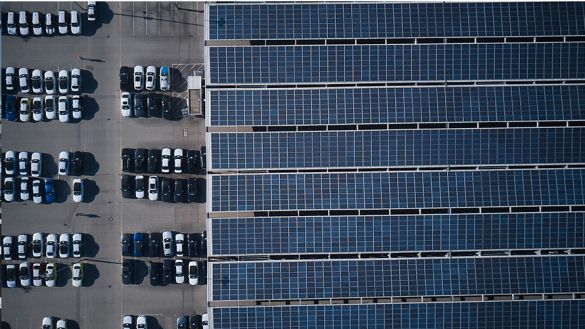
BMW Group Plant Dingolfing.
A front-runner thanks to radical measures: as the largest vehicle plant of the BMW Group in Europe, the Dingolfing plant has been able to record a fall of one third both in resource consumption and in emissions within the last ten years, thanks to the use of innovative production technologies and production equipment. In these endeavours, the new energy centre is relying on the highly efficient generation of electricity and heat with the aid of a combined heat and power plant (CHP). It converts gas into electricity and exploits the heat resulting from the process as a source of energy. Thanks to the CHP station and one of the largest photovoltaic rooftop systems in Germany, the plant now produces almost half of its own electricity demand. It covers the remaining demand exclusively with green electricity from external energy providers. In waste and disposal management, in particular, the aspiration for a company-wide sustainability strategy is high. Here too the Dingolfing plant achieves top values thanks to efficient recycling measures such as the innovative pressing plant with an impressive recycling rate of 99.8%.
BMW Group Plant Shenyang.
More innovations, fewer emissions. Alongside our production locations in Europe and Brazil, for which we already purchase electricity exclusively from renewable sources, our works in Shenyang has the most efficient photovoltaic plant of the BMW Group to date with a peak output of 15.1 megawatts.
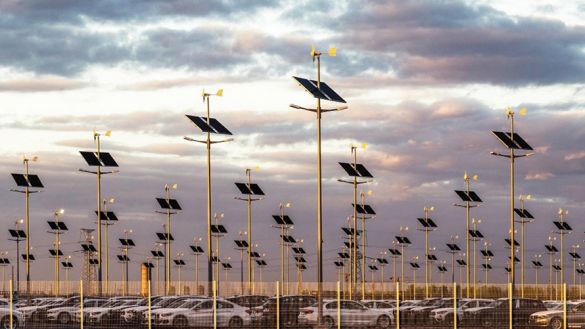
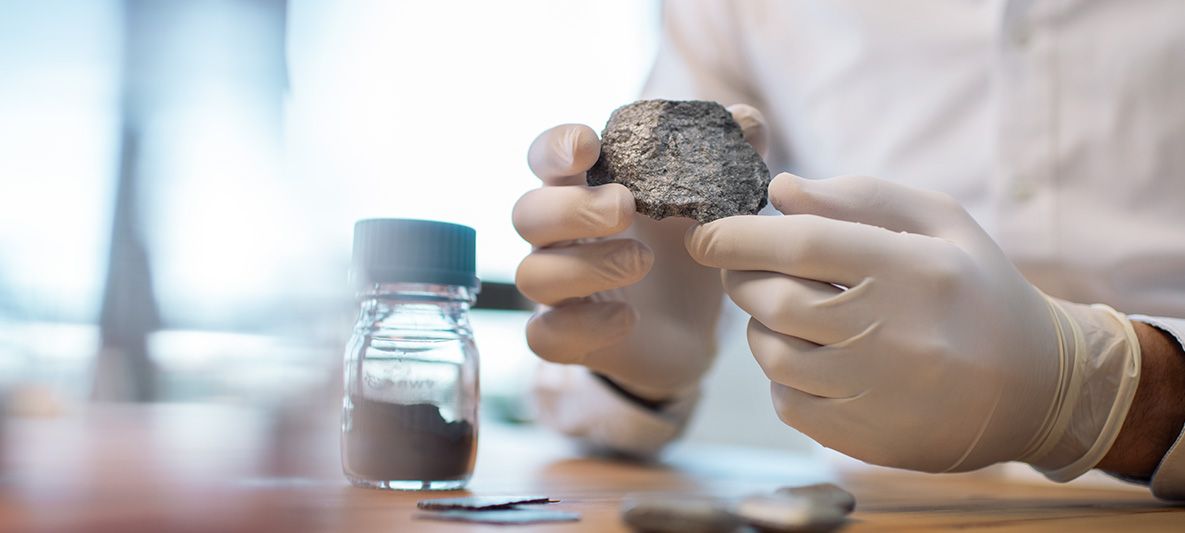
RESPONSIBILITY IS OUR DRIVE.
With projects like ‘Cobalt For Development’ we are bringing our sustainability strategy into our surroundings step by step and hence into all stages of our value-added chain. Through our guidelines, but also through support and promotion, we can ensure that our partners in the supply chain also systematically meet our high social and environmental standards.
OUR HIGH-VOLTAGE BATTERIES: A SUCCESS STORY.
Reusing our battery cells.
Efficient down to the last volt: We are taking back all used BMW high-voltage batteries worldwide – even though there is no legal requirement to do so. During their “second life” our vehicle batteries are put to use in stationary storage systems, with which we are successively equipping our locations around the world. In this way, we are integrating renewable energies into the electricity grid, increasing its stability and lowering the energy costs for consumers. And we are progressing further towards the target of locally CO2-free production. The best example of this is our BMW Group plant in Leipzig with a storage farm consisting of about 700 BMW i3 batteries. As buffer storage for renewable energies, they are helping to store surplus wind energy and then integrate it back into the electricity grid. In addition, they are also decreasing the energy costs for production.
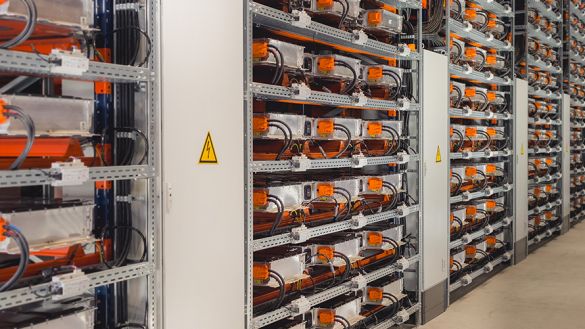
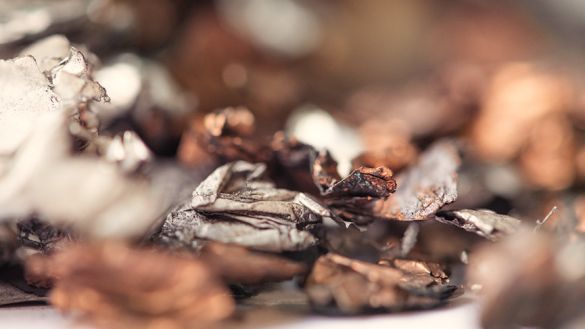
Recycling our battery cells.
In the case of batteries that have exceeded their useful life as stationary storage, too, we are achieving a constantly rising recycling rate for the valuable resources. This yields particularly high-quality recycled materials for the production of our new lithium-ion batteries. We have partnered with German recycling specialist Duesenfeld to develop a method that can achieve a recycling rate of up to 96% of the materials – including graphite and electrolytes. Currently, only thermoplastics wetted with electrolytes remain after the process. Currently, only thermoplastics wetted with electrolytes remain after the process.
Resource efficiency of our suppliers.
Trendsetting even before production: As a pioneer in sustainability, our word also carries a lot of weight with our suppliers - and we make use of it. We have a contractual agreement with our cell manufacturers that only green electricity will be used in the external production of our fifth generation of battery cells. This will lead to a total saving of around 10 million tonnes of CO2 by 2030 and is roughly equivalent to the amount of CO2 that a city of one million inhabitants such as Munich emits each year. As a participant in the Carbon Disclosure Project (CDP), we support our suppliers in taking measures to reduce CO2 emissions and increase the share of renewable energies.
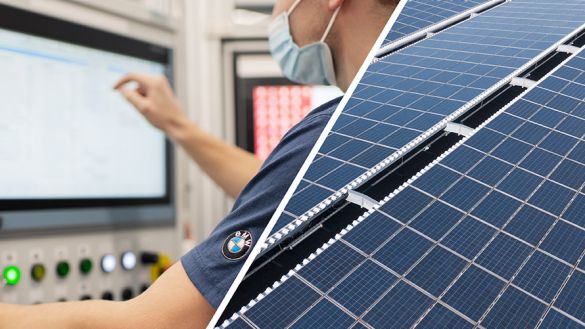